RAG – Renewables and Gas
RAG Austria AG is Austria’s largest energy storage company, and one of Europe’s leading gas storage facility operators.
Our business focus is market driven storage, conversion and conditioning of energy in gaseous forms.
We also develop leading edge energy technologies related to green gas like hydrogen that partner renewables.
“We have been shaping the energy world for nine decades, successfully ensuring security of supply, driving innovation and pointing out new paths and prospects for the future.”
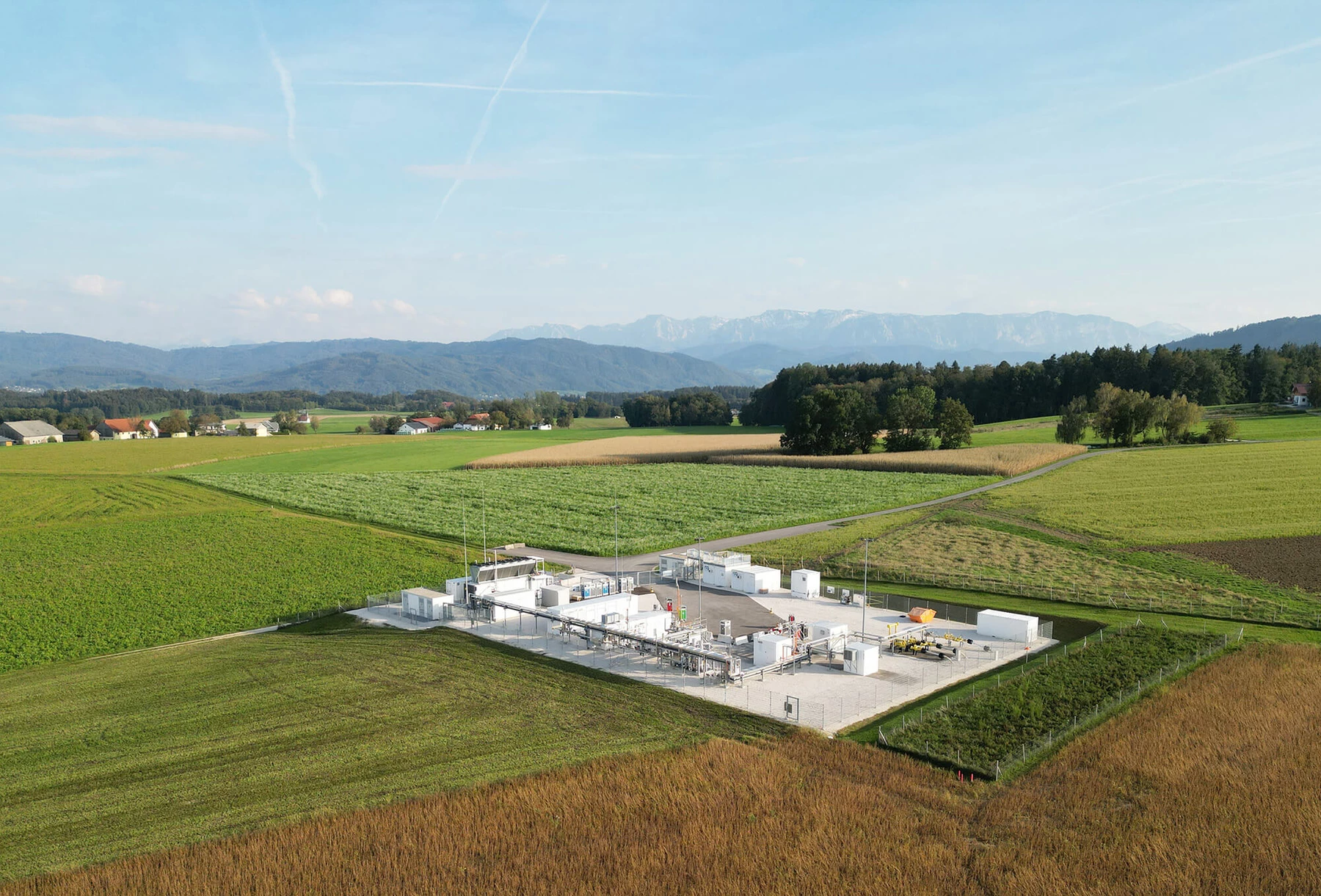
RAG Austria AG and ENERGIEALLIANZ Austria focus on green hydrogen
From June 2025 until the end of 2026, the hydrogen plant will be supplied with three gigawatt hours of green electricity from 100 percent Austrian renewable sources every year. Through this cooperation with RAG Austria, ENERGIEALLIANZ Austria is strengthening its commitment to green hydrogen as a central component of the Austrian energy transition.
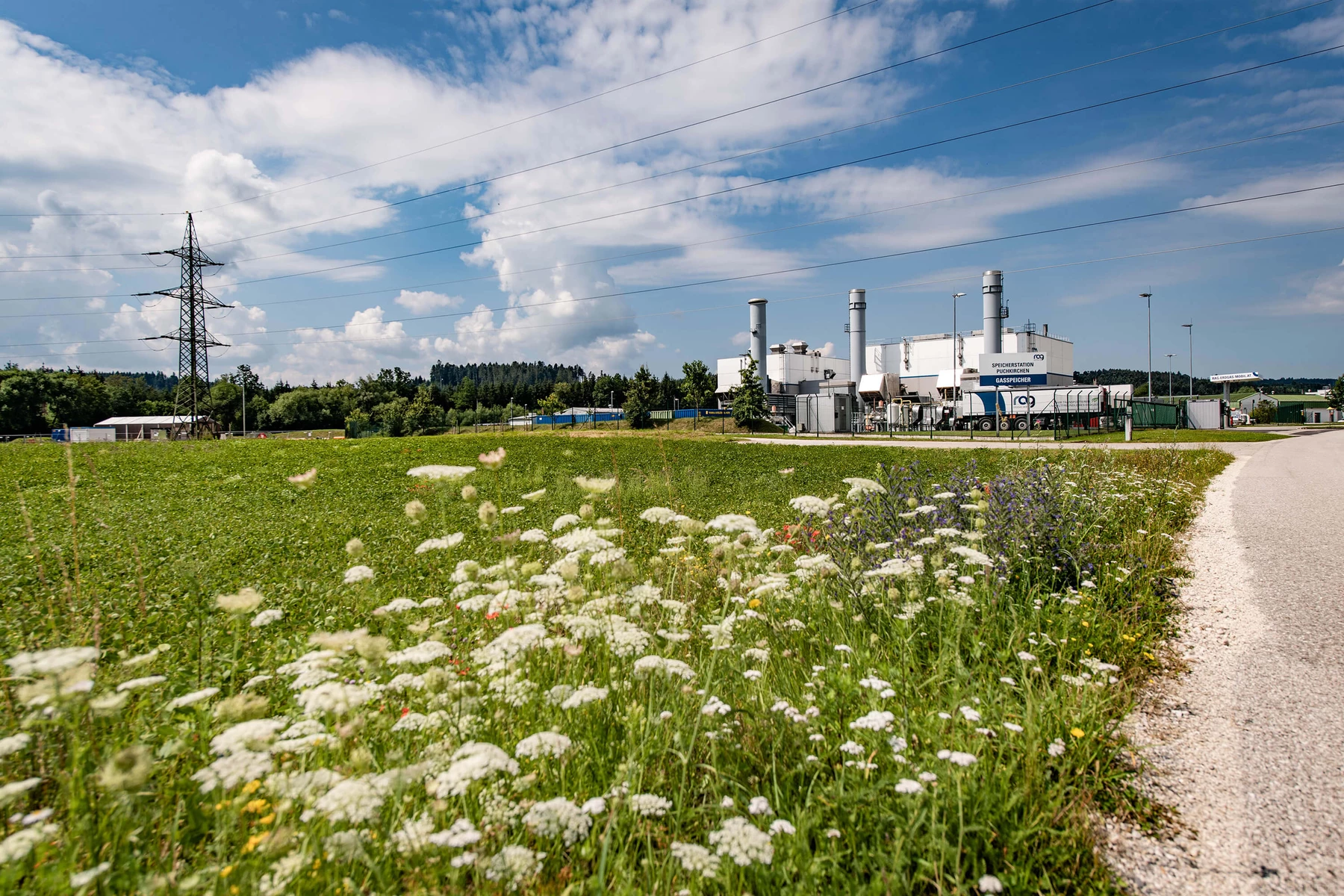
Seasonal electricity storage in the form of hydrogen ready for scale-up
The demo operation of hydrogen production and storage in the USS2030 project has been successfully completed, showing that it is technically possible to offer hydrogen storage services on a scaled and commercial basis in depleted underground gas reservoirs.
In 2023, the world's first hydrogen storage facility was opened in an underground sandstone gas reservoir as part of the flagship project Underground Sun Storage 2030 (USS 2030) in the municipality of Gampern, Upper Austria. The project operation, consisting of two storage cycles, has been successfully completed.
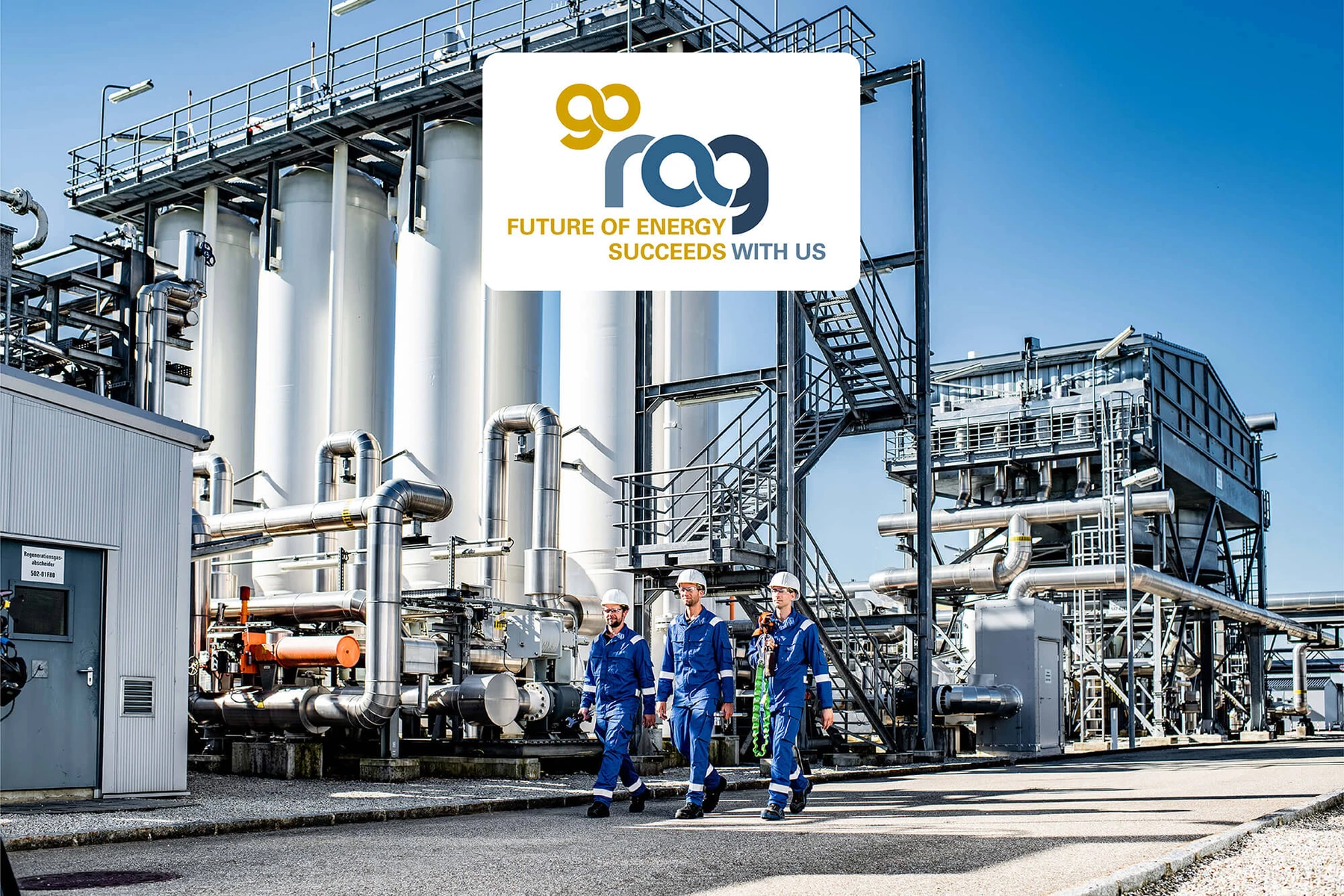
Shaping the future of energy – for 90 years
RAG Austria AG has played a decisive role in shaping the Austrian energy landscape for 90 years now. Founded as “Rohölaufsuchungs-Gesellschaft”, our roots are in crude oil and natural gas production in Austria. Based on this, we have developed into one of Europe’s largest energy storage operators: reliable, safe and flexible. Today, RAG stands for ‘Renewables and Gas’: we have transformed ourselves from a traditional production company into a pioneer in storage and security of supply and are strongly committed to a sustainable energy future.
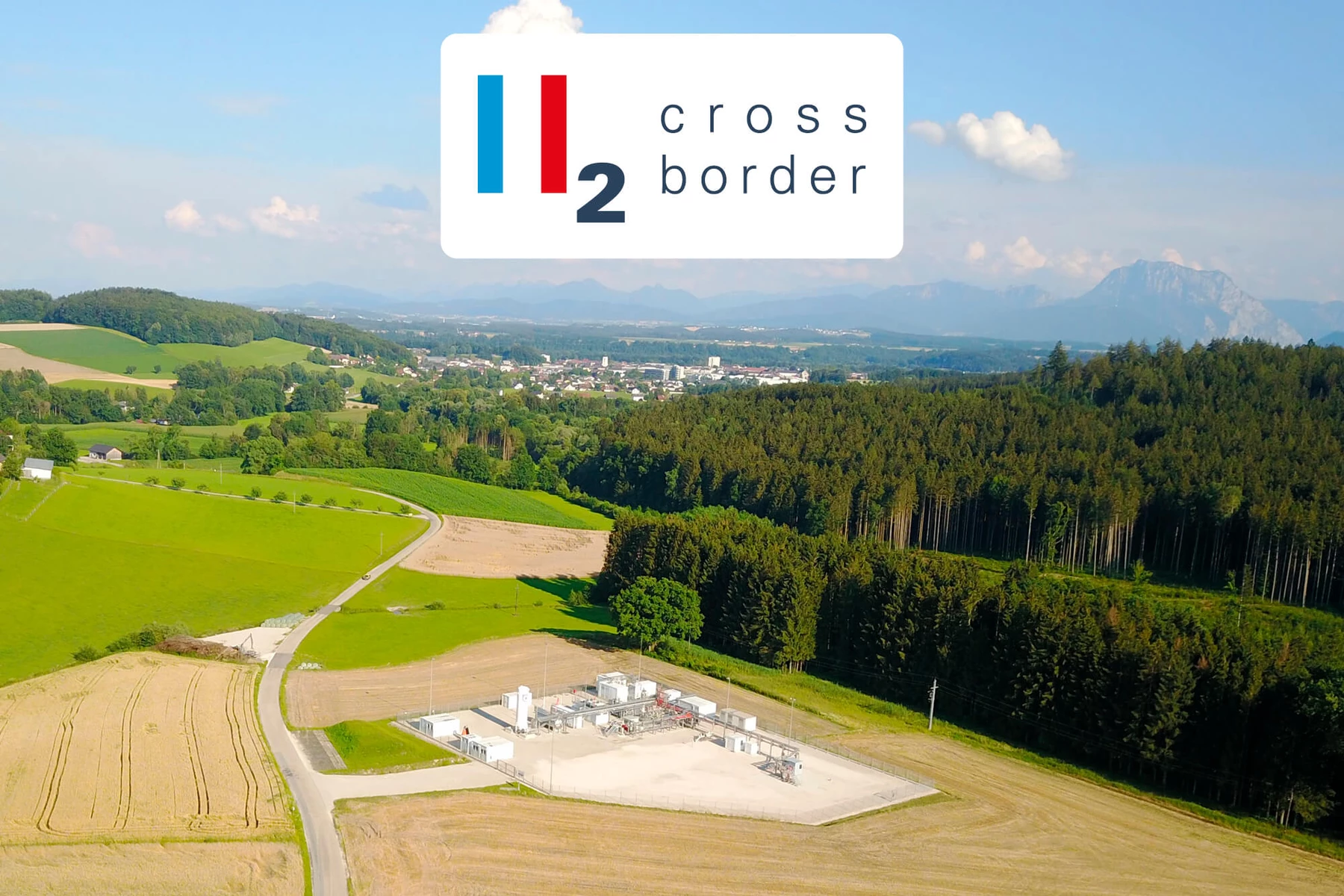
„H2 cross border“ – Hydrogen does not know any borders
First pipeline-based hydrogen delivery from Austria to Germany
The hydrogen ramp-up in Europe needs real cross-border projects. This is why bayernets GmbH, Bayerngas GmbH, MEGGLE GmbH & Co. KG, RAG Austria AG and Shell Energy Deutschland GmbH have launched the project "H2 cross border".
The project partners have now succeeded in implementing the first hydrogen delivery from Austria to Germany under the current framework conditions and rules.
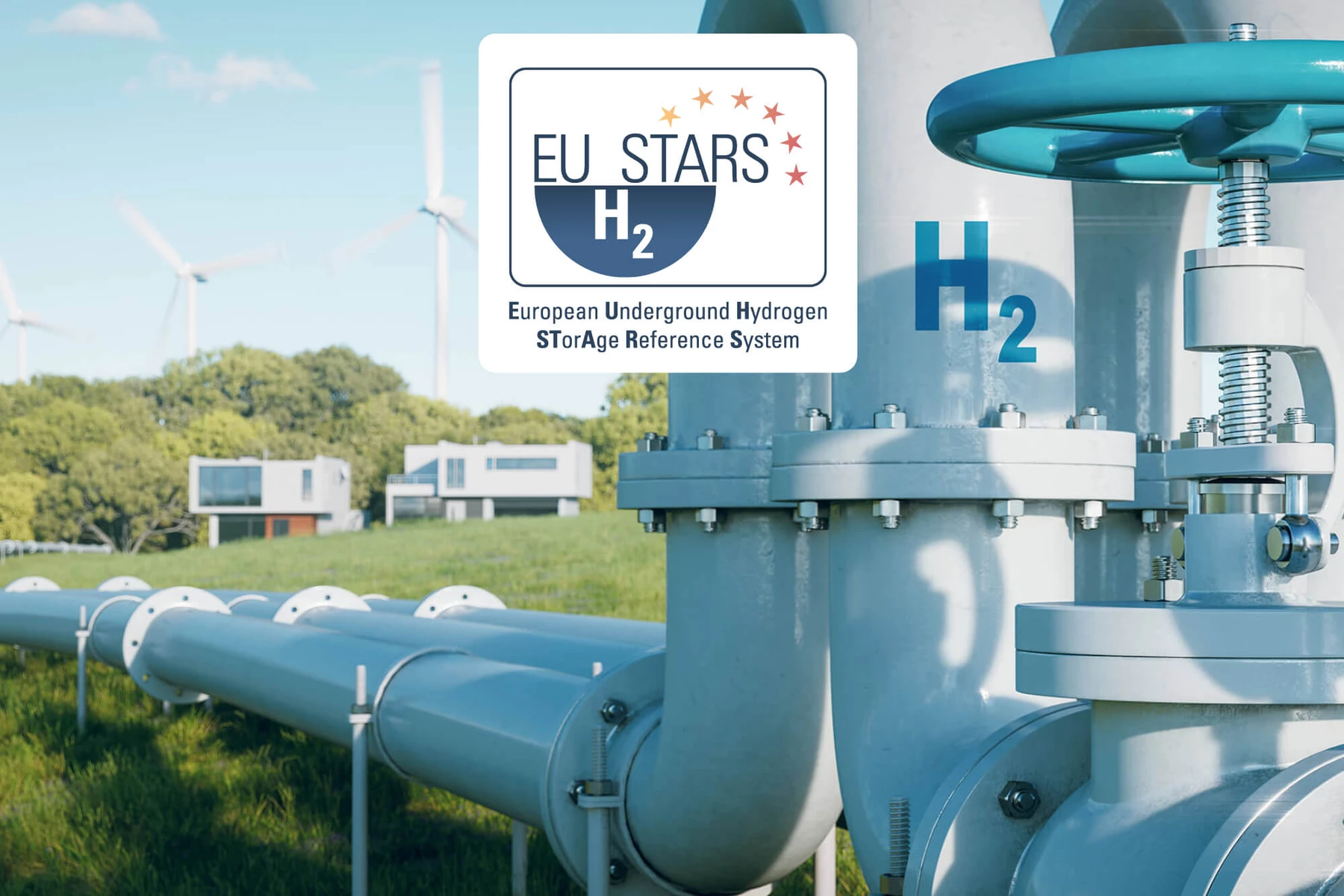
Start of European Reference Project EUH2STARS for large-volume hydrogen storage
Paving the way towards the future of European underground hydrogen storage
THE EUH2STARS is a European flagship project for the development of marked-ready underground hydrogen storage (UHS) in depleted porous natural gas reservoirs and for building the infrastructure for hydrogen storage. The project is supported by the Clean Hydrogen Partnership.